Managing the turbulence on-ground
The last one year has been extraordinarily difficult for the ground handling industry.
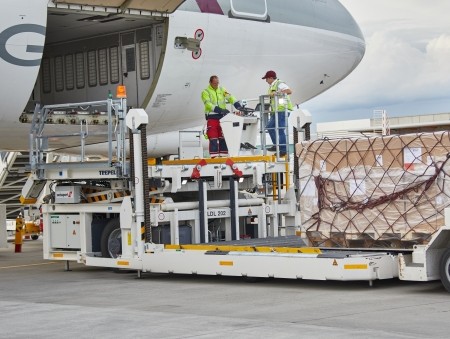
The last one year has been extraordinarily difficult for the ground handling industry. 2021 will be another challenging year with continued solid demand for quality and safe cargo services and innovative solutions that deliver value. Market players are going to focus more on digitalisation, sustainability and will deploy skilled manpower for optimal supply chain processes.
Covid-19 has essentially wiped out airline demand for the classic ground services business since March last year. While it is going to be some time before the aviation industry returns to the levels witnessed pre-Covid, it presents significant challenges for all stakeholders, including handlers.
“Pre-Covid, the main concern was the poor rates commanded by the industry which stifled essential investment. Now that rates have recovered and look like holding at more viable levels, our focus as an industry must shift towards better facilities for pharma and greater uniformity in handling processes and standards,” said Wilson Kwong, chief executive, Hactl, Hong Kong’s leading cargo handling company.
With the world’s top priority being the transportation and handling of medical aid and vaccines, ground handlers are doing their best to provide customers with more visibility and self-service options, and to deliver much-needed operating efficiencies.
“WFS was already ahead of the game because we have been investing over the past 2-3 years to support our customers’ premium products for pharma cargoes,” said Barry Nassberg, group chief commercial officer, Worldwide Flight Services (WFS).
Now that rates have recovered and look like holding at more viable levels, our focus as an industry must shift towards better facilities for pharma and greater uniformity in handling processes and standards.
Wilson Kwong, Hactl
WFS now has 15 dedicated pharma facilities in Amsterdam, Bangkok, Barcelona, Brussels, Cape Town, Copenhagen, Cork, Dublin, Frankfurt, Johannesburg, London, Madrid, Miami, New York JFK, and its €10 million state-of-the-art Pharma Centre at Paris CDG. WFS’ facilities are either IATA CEIV or Good Distribution Practice (GDP) certified or compliant, with specially-trained teams in each location to provide a range of value-added services. “We created WFS’ Project Coldstream to co-ordinate our response to the global transportation of Covid vaccines and our team of experts are continuing to work closely with airlines, forwarders and logistics providers, government agencies and industry organisations such as Pharma.Aero and The International Air Cargo Association (TIACA) to ensure the integrity of vaccines shipments is maintained, and they are handled quickly and securely in order to reach people around the world without any delay,” added Nassberg.
Similarly, Swissport has already been investing in pharma infrastructure. Last year, the company took the step to implement its Swissport Pharma Center brand, which encompasses not only infrastructure but as well other aspects of the pharma handling processes. “We kicked off extensive preparation processes for the transport of vaccine shipments and have taken the necessary steps to ensure that whatever can be prepared, is prepared,” revealed Hendrik Leyysens, VP global operations - cargo, Swissport.
Talking about the major steps implemented by Turkey-based ground handling major Celebi Aviation, Funda Eraslan, global marketing and communications manager said, “We have directly initiated the application processes for IATA CEIV Pharma Certification in all our cargo stations; Istanbul, Delhi, Frankfurt and Budapest. We have successfully completed all steps and audits in Budapest and received our CEIV Pharma certificate. Other subsidiaries’ processes are continuing and will be finalized until the end of 2021.”
We will also continue to invest in training to upskill and reskill our staff in an effort to further optimize our resources and maximize efficiency across our operations.
Bernd Struck, dnata
From operational perspective, we have improved our infrastructure for the handling of vaccines and medical aid. For ensuring the safest and fastest transportation of these vaccines, Cool Dollies are deployed, whole dry ice transportation process is reviewed, and necessary arrangements are done, our handling capacities are increased for the storage of cargo -70 Celsius.”
Dubai-headquartered dnata has invested significantly in its cold chain and pharma-handling capabilities in recent years. “We are well positioned to move every pharma and vaccine shipment safely and efficiently, in compliance with the highest international standards. Our certified warehouses are capable of handling large volumes and can be further expanded when demand increases, likely in the second half of the year. We are working closely with our partners and have joined forces with Dubai Airports and GMR Hyderabad International Airport to support them in creating a focussed Covid-19 vaccine distribution corridor,” divulged Bernd Struck, senior vice president – UAE Cargo & DWC Airline Services, dnata. Since March last year, dnata’s teams have handled over 5,000 cargo-in-cabin flights, safely moving 50,000 tonnes of in-cabin shipments at DXB.
Meanwhile, Hactl has been 100 percent pharma-ready for several years, having invested heavily in its temperature controlled facilities, training and procedures even before the advent of WHO GDP and IATA CEIV Pharma – being incidentally the first in Hong Kong to achieve these certifications. “Our facilities have large scale capacity, are fully-compliant, and our ‘Golden Route’ pharma fast-track ensures the fastest possible transition from aircraft to waiting vehicles. We are, therefore, ready for whatever vaccine traffic arrives in Hong Kong,” said Kwong confidently.
Need for digitalisation, data exchange and transparency
While infrastructure planning is of the essence, the industry also needs to speed up digitalisation to nurture the growth of e-commerce, in which exchange of data and transparency are essential.
“On the one hand, there is the ever-increasing speed of technology development in logistics industry which needs new processes being implemented for which no standard has been set. This creates quite some challenges for all parties in our industry and we need to find creative solutions for,” said Swissport’s Leyssens.
Speaking about the digitalisation initiatives at WFS, Nassberg said, “We have various projects at different stages of development. Our new cargo terminal at Brussels Airport, for example, is using kiosk and slot booking apps to eliminate truck waiting times when drivers drop off or collect cargoes. This is part of the Air Cargo Belgium community initiative, which is an impressive model for other airport cargo communities.”
Cargo handler dnata continues to invest in cutting-edge technologies to further improve efficiency and offer more value to its customers. “We will redevelop our cargo community platform, Calogi, to provide one-stop services, including appointment and customs services management, to the air cargo community. As a result of a recent investment, our just-in-time freight handling platform, which seamlessly integrates into Calogi, will reduce the average freight handling time at our cargo terminals by more than 60 percent to an average of 30 minutes,” said Struck.
Skilled manpower for efficient cargo handling
For a people’s business like ground handling, creating the best and safest working environment for each co-worker is of the essence. Not just that, given the sensitive nature of varied shipments, ground handling companies need to make sure that they educate their workers and train them on how they should handle different types of shipments.
“At Swissport, we are constantly taking steps to attract industry talent - whether it’s by making changes to the working environment, offering internal career opportunities or leadership development. Additionally, we are focusing on giving our colleagues the tools they need to execute their day-to-day activities. We are deploying many new technologies to support them and make their work easier. Next to that we are highly focused on training delivery – our fantastic training set-up is well-recognized by many industry partners and helps us to boost internal process knowledge and compliance,” said Leyssens.
We kicked off extensive preparation processes for the transport of vaccine shipments and have taken the necessary steps to ensure that whatever can be prepared, is prepared.
Barry Nassberg, WFS
WFS, Nassberg says, takes the hiring, training and retention of its workforce around the world extremely seriously. “In this, we are supported by our WFS Academy, which has been accredited by IATA as one of the world’s top 10 aviation training providers.”
“Of course, the fact is we are also operating in a very tight margin industry, so we are constantly facing challenges from other industries when it comes to recruitment. This is why we try to achieve the lowest possible staff turnover. We invest in our people to give them the knowledge and skills they need, and the experience they gain is of such value to us and our customers. We don’t want to lose that,” he added.
But manpower remains a constant challenge to make sure the company has the right level of resources, at the right times, in the right places to provide the highest standards of safety, security and service its customers need, alongside the need to make a profit for its shareholders and to be able to invest in modern facilities, equipment, and technologies.
“We will also continue to invest in training to upskill and reskill our staff in an effort to further optimize our resources and maximize efficiency across our operations,” said dnata’s Struck.
Hactl’s long-term policy of continuous improvement has always imposed a duty upon the company to train its staff to the highest possible standards. And qualified workers are confident and happy workers. “We have our own in-house training facilities occupying an entire floor of our large office building; we utilise VR for pre-training new recruits for potentially hazardous ramp work; and we are an accredited IATA DGR training provider. Training is at the very core of our recruitment, personnel development and staff retention policies. We cannot and do not rely upon others to train operation staff for us to recruit: we therefore “grow our own”. This also avoids reliance on temporary unskilled labour,” said Kwong.
Celebi offers its own training and development programme for its employees. “After the establishment of Çelebi Aviation Academy, we have started to invest more on training and related implementations for the last few years. As a result of these developments, we have been awarded as the first ground handling company in the industry to achieve the IATA Training Validation Program (TVP) certification. Also, during the pandemic period we have continued our training programs though our online e-school program. In addition to that we have invested in Virtual Reality modules and provide operational trainings in digital platforms,” said Eraslan.
Going forward
Despite being in a very uncertain period for the aviation industry in terms of its recovery from the Covid disruption, the second half of 2021 is expected to see the start of a recovery in terms of the number of passenger flights as lockdowns and travel restrictions are eased. Ground handlers need to be extremely agile so they are ready for new opportunities when they come along. In 2020, the challenges came thick and fast, and daily. During Covid, for example, there have been so many cargo-only flights by passenger airlines, initially to support movements of PPE, and, of course, to generate revenues. Ground handlers have had to respond to the needs of airlines and airports at very short notice. It was a perfect storm of running a business where many staff were working from home, which created communications and IT issues; of introducing new measures to keep staff safe from infection; of dealing with unprecedented and unpredictable work peaks at all hours; and of working with reduced teams due to safety measures.
“One of the challenges we don’t often see people talking about is the need to be profitable. We have a very cost-intensive global business, which we are constantly looking to improve and make more efficient. To do this, we need to be able to invest, and to justify investments they must be profitable. That’s the same for every well-run business,” said Nassberg.