IAG Cargo gives a lowdown on how to set up a cargo operation in 7 days
IAG Cargo gives a lowdown on how to set up a cargo operation in 7 days
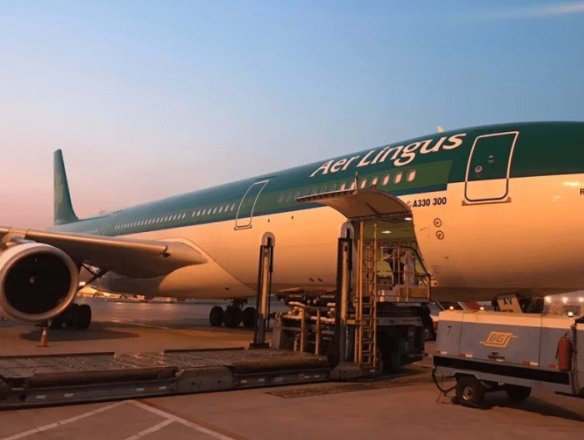
It’s not every day that a sudden Saturday night phone call kickstarts an unprecedented logistical marathon, but in a rapidly changing world where a soaring demand for essential supplies and critical deadlines are head-to-head, the world of cargo is facing a new set of challenges.
In the case of IAG Cargo, this marathon has been more of a sprint, and a hugely successful finish for our teams across the globe who have stopped at nothing to get there in just a matter of days. Our continued effort in the fight against Covid-19 has included standing up an entirely new operation out of Beijing to provide Ireland’s hospitals and medical facilities with crucial PPE over the coming months.
Loading the passenger aircraft with cargo
Having been contracted by the Health Service Executive of Ireland, overfly rights and approvals were secured by Aer Lingus in record time from the Irish Aviation Authority (IAA), along with permits and landing slots at Beijing Capital International Airport (PEK). It was then over to IAG Cargo to coordinate this brand-new supply chain. But, where exactly do you start when there is no equipment, people, systems, contracts or suppliers in place, and an initial schedule of around 60 flights due to begin in less than a week’s time?
Sourcing a ground handling partner at PEK was the first step, although this would not be any normal ground handling operation. Thanks to Aer Lingus engineers, the Irish Air Line Pilots’ Association (IALPA) and its Safety and Technical Committee, as well as the IAA, an ingenious procedure involving specially made bags and straps was born to ensure that cargo could be loaded in both the cargo hold and the passenger cabin.
Firman So, IAG Cargo’s area customer service manager for Hong Kong, China, Philippines and Taiwan explains, “It was crucial that we found a partner capable of supporting our brand-new cabin loading procedure to ensure we could safely and securely utilise the full capacity of each aircraft. We were fortunate to find an excellent partner in Beijing Aviation Ground Services in such a short timeframe.”
IAG Cargo’s operational teams in Dublin work seamlessly with Aer Lingus to unload each aircraft immediately upon arrival
With cabin loading preparations well underway, the next challenge would be to manage the speed of the aircraft turnaround. Due to the current entry restrictions in China, all Aer Lingus crew, comprising five pilots, two engineers and a loadmaster, would be required to remain on board the aircraft in Beijing which meant limiting the turnaround time to four hours.
Under normal circumstances, the goods due to travel in the cargo hold would be built onto ULDs, netted and staged by the aircraft parking bay ready to be loaded immediately. With no ULDs on hand at PEK, however, our local team used the days leading up to first flight to transfer existing stock from our British Airways base at Beijing Daxing International Airport (PKX) – a huge win, especially in light of the current road transport restrictions in China and one that enabled our team to have all cargo built and prepared 48 hours before the initial flight landed.
Systems and messaging came next, and with testing complete, close coordination between our local IAG Cargo team, the IDA (Industrial Development Agency), the manufacturer and their freight forwarder ensued to organise a steady and sustained flow of goods into our warehouse. Armed with this new stock of ULDs, our team was able to accept and pre-build up to 15 flights worth of cargo to accommodate the schedule which was due to quickly ramp up to five flights a day.
At the other end, our operational teams in Dublin lay in wait, working seamlessly with Aer Lingus to unload each aircraft immediately upon arrival before passing the goods over to the Irish Defence Forces who had been tasked with distributing these essential supplies across Ireland.
This is just a snapshot of some of the incredible feats achieved by all of the teams involved, and with the first batch of PPE on this program due to weigh in at a spectacular 630 tonnes, it will be extended in the coming months. On top of that, it has been hugely important in laying the framework for various other operations launched by IAG Cargo in the past few days and weeks, not least in launching a brand-new operation out of Shenzhen – a first for IAG – in just 72 hours to support the transport of urgent PPE into Spain with Iberia.
Commercial and operations teams have coordinated day and night to cover every step of the process – from setting up new customer accounts with a plethora of forwarding agents all requiring their own specific needs and requirements, to ensuring cargo is handled to IAGC standards from thousands of kilometres away.
Lee Adams, area commercial manager, said, “The real test of teamwork comes when the challenge is unexpected and unprepared for and I can honestly say that every single member of the China team has risen to this challenge head on. I am extremely lucky and proud to have such individuals in all departments as colleagues.”
The dedication and remarkable teamwork across the group and wider network is an important reminder that we’re always moving – and upping our personal bests.
(This article was originally published on IAG Cargo’s digital magazine)
Disclaimer: The views and opinions expressed in this article are those of the author/company and do not necessarily reflect those of STAT Media Group.