FROM MAGAZINE: Why it’s time to bring digital transformation down to earth
The digital transformation appears to be on the rise in the supply chain community and it will ultimately transform supply chain. Maria Jesus Saenz, James Rice Jnr. and Ken Cottrill argue that it’s time to bring digital transformation down to earth. Delirium Tremens, or the DTs, is a condition that causes “delirium, tremor, anxiety and […]
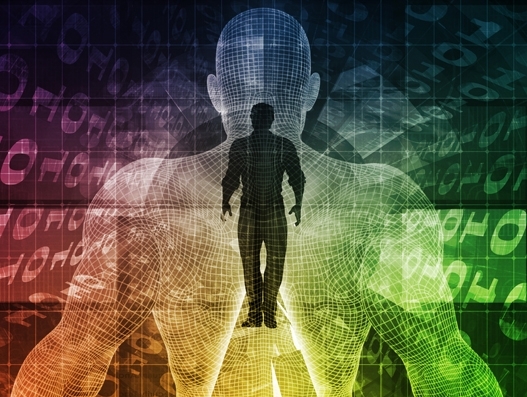
The digital transformation appears to be on the rise in the supply chain community and it will ultimately transform supply chain. Maria Jesus Saenz, James Rice Jnr. and Ken Cottrill argue that it’s time to bring digital transformation down to earth.
Delirium Tremens, or the DTs, is a condition that causes “delirium, tremor, anxiety and vivid hallucinations,” according to one dictionary definition. It’s a symptom of alcoholism, but there is another type of DT, digital transformation, caused by the excessive consumption of hype, not alcohol.
The Digital DTs appear to be on the rise in the supply chain community.
This is fed by predictions that we are on the cusp of fully automated supply chains, and dire warnings that companies need to get on the bandwagon fast or be left behind. Some of these predictions border on the hallucinatory. And they can cause anxiety as supply chain professionals fret over their lack of progress on the DT front.
Before practitioners start preparing for mass unemployment because supply chains could become smooth-running, self-regulating utilities within the next 5 to 10 years as one recent article suggests, they should take a step back. The idea that DT will render human expertise redundant in that time frame is surely nonsense.
Impediments to the vision
Undoubtedly, digital transformation (which we’ll call DT from now on) is a major thrust for companies inspired to instigate change, that will ultimately transform supply chains. But it will take decades for most companies to create the self-regulating utilities that automatically source raw materials and components sustainably, turn them into products, and deliver the products unerringly to delighted consumers with negligible human intervention. Indeed, such a vision may never be realized for some enterprises.
A major reason why the vision is unrealistic is that increasing complexity is driving the need for companies to continuously redesign their supply chains. This complexity comes in countless forms such as the growth of online marketplaces, omni-channel distribution challenges, automation, developments in sensing technology, energy market volatility and growing compliance requirements.
Automating processes that are invariably changing in ways that we have not been able to predict makes DT a work in progress. You can digitally transform and automate what you have today, but that model will likely not serve you tomorrow.
Another challenge to the DT vision is the need to build core digital infrastructure first. A leading company we engaged with recently to do a deep dive into the mechanics of DT likens the journey to building a new city. Before the buildings can be created, it is necessary to develop the infrastructure; the roads and drainage systems that will connect the new community and enable it to function efficiently. In the case of DT, that involves replacing expensive legacy systems and creating the digitised information pathways that will underpin the new entity. That takes time, effort, money and the cooperation of many diverse stakeholders. Meanwhile, companies have to run their existing businesses.
Difficult balancing act
The bold companies that choose this path must strike a balance between the long-term task of building IT infrastructure as well as aligned end-to-end data structures and meeting the daily IT needs of their businesses. Implicit in this choice is deciding whether the central database should be used for centralised decision-making (à la control tower) or to facilitate decentralized decision-making and 20/20 supply chain visibility.
We believe it takes a rare combination of resolve and fortitude to meet these goals.
A company on this path we met recently highlighted another potential conflict: the need to rationalise requests for data to make way for DT projects. A worry is that if operations can’t get the data it wants from IT, people may choose to go rogue and create data systems of their own?–generating even more complexity. Or even worse, creating a need to invest in more data management resources.
Additionally, DT is not a self-contained, well delineated package of services and best practices that companies simply adapt to their business models and plug in. It is an ill-defined, continuously evolving swarm of options, that companies must evaluate carefully before choosing the options that best suit their organisations and competitive goals.
Companies may be better served if they think of DT as an aspirational notion. Such a notion is intended to leverage data and technology to accelerate and automate business operations, using insights from analytics to improve forecasts and enable rapid response to those forecasts where possible. And DT-related supply chain redesigns should not revolve around the reduction of human intellect.
Where to start
As we’ve learned from talking with many companies, the journey has various starting points.
Some companies start from the customer side. They create apps to generate advanced digital value propositions for a set of customers who are amenable to the digital experience. This approach is predominant in the retail industry, where the shopping experience is shaped by historic buying patterns and the desires of each shopper. These data-driven efforts downstream bring opportunities to apply digitalisation upstream in the value chain.
A company in the apparel industry decided to get its feet wet by plunging into a DT project. Before taking the plunge, they took time to select a pain point that needed to be addressed, and would involve at least one partner they could learn from. Also, they wanted a joint project that could provide a platform for other DT initiatives. In other words, the company wanted to find the right teacher for a very complex lesson.
In fact, nearly all of the examples that we have observed have come from narrowly focused applications of DT. The ‘dip-your-toe-in-the-water’ approach requires smaller investments and can be applied to the most challenging issues. If the projects are successful, they are easier to scale than more ambitious efforts. For example, a consumer goods company produced most of its product in low-tech facilities and suffered from a high rate of quality defects. Rather than automating the entire production operation, the company focused on the quality inspection process which had been done manually and qualitatively. Some simple fixturing allowed automated quality assessments and measurements and rapidly identified the pattern and source of the defects.
A company in the electronics business took a more systematic approach. It started with an overarching vision to improve the experience of customers, suppliers, and employees. Next, the enterprise identified 180 use cases which were narrowed down to 80 in 23 broad groups. Through a series of internal workshops, they prioritised the projects. Interestingly, this exercise was not guided by formal estimates of financial ROIs. Also, the company set up an internal organisation that was responsible for ensuring that every department was kept in the loop, to avoid unintended consequences as one department forges ahead in isolation. It realized that the early focus should be on efficiently and dynamically connecting all supply chain actors?–?not on the technologies required.
There are advantages and disadvantages to each approach. Piece-by-piece projects can deliver quick wins, but create a Frankenstein-like collection of DT applications that may not fit together well or serve the organisation’s goals. Alternatively, large, company-wide DT renewal initiatives may not deliver progress quickly enough and can drain the company’s financial resources before yielding an ROI. However, if the company possesses the patience and financial resources to execute company-wide transformation, this can be a better approach for achieving its long-term objectives.
Grounded in realism
The type of DT applications that companies have pursued is just as varied. The companies we’ve talked to have used DT projects to create a platform for fashion designers, automate procurement processes and streamline trade regulation compliance, to name but a few initiatives.
In general, they were prepared to fail fast, to constantly revise their approaches as they internalized the lessons learned, and gained senior leadership support for their efforts. And they learned that regardless of the approach taken there are certain challenges that can’t be avoided, such as the need to adapt processes, integrate data streams and connect with decision-making engines based on human intelligence.
They’ve encountered obstacles such as entrenched legacy systems and resistance to change, and a scarcity of digital talent. But rather than becoming distressed at the challenge of such hurdles, they see them as part of the learning experience that guides them towards the right path.
That is not to say that these companies are well on the road to a fully-fledged, digitally transformed supply chain (whatever that is). Rather, they have started a journey that might never end in the foreseeable future but will provide wins along the way that continue to propel them forward.
And yes, they may experience anxiety and even tremors as their organizations struggle to accept the changes that must be made. But they avoid hallucinating about what DT is supposed to achieve and where they need to be on DT’s ever-changing evolutionary path.
Dr. Maria Jesus Saenz leads the MIT Center for Transportation & Logistics’ (MIT CTL) Digital Supply Chain Transformation Initiative (Digital DC); James Rice Jnr. is the Deputy Director of MIT CTL and Ken Cottrill is the Global Communications Consultant for MIT CTL. This article was originally published in the blog section of MIT Center for Transportation and Logistics (ctl.mit.edu)