What it takes to create the world’s largest digital ULD fleet
With accelerated focus on digital transformation, Unilode, with its multiple partners on board, is creating the world’s largest digital ULD fleet.
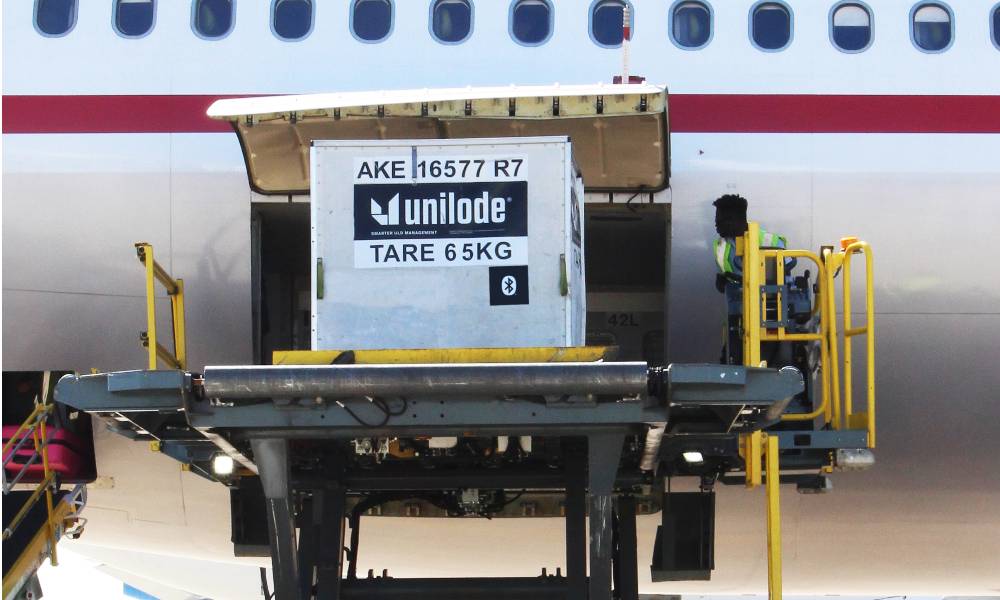
At the turn of the current millennium, a project team under Swiss Cargo studied the feasibility of pooling unit load devices or ULDs with partner airlines with the aim of reducing costs and improving efficiencies. Two decades later the concept is a reality after several ownership changes and brand identity. Unilode Aviation Solutions, headquartered in Zurich, Switzerland, manages the world’s largest outsourced fleet of ULDs and owns the largest global network for the maintenance and repair of containers, pallets and in-flight food service equipment. With accelerated focus on digital transformation, Unilode, with its multiple partners on board, is creating the world’s largest digital ULD fleet. Benoît Dumont, chief executive officer, Unilode, speaks to Reji John in an interview about the current trends in the ULD market and how the company is positioning itself as the market leader. Benoît, a professional with more than two decades of leadership experience in global logistics and supply chain multinational companies, joined Unilode as its CEO in 2017, the year CHEP Aerospace Solutions rebranded itself as Unilode Aviation Solutions.
What according to you is the potential for growth and revenue in the Unit Load Device (ULD) market?
Unilode is convinced that in the coming years the industry will remain in a challenging time. This does however still provide some possible growth and revenue opportunities. As cargo demand is expected to stay strong for a long time the dedicated cargo carriers and integrators will most likely continue to grow and expand their business. Healthcare and pharma logistics, which is partially vaccine-related, will be another source of stability and possible growth and Unilode has a strong presence in these supply chains. With our worldwide network we support our globally operating partners and can quickly extend to other locations to meet their needs and add value to their business, with the most recent example being the addition of Beijing to our MRO operations.
Airlines are facing a number of serious ULD-related challenges associated with the ownership of the ULDs, such as storage of excess containers and pallets, fleet availability and repositioning of equipment with fewer options at their disposal. Currently we see airlines reduce their ULD repairs to mitigate costs although this might lead to a future cost increase when the market picks up. It might also cause equipment shortages going forward. In addition to ULD repairs Unilode provides ULD management solutions and while we also face stronger challenges now than pre-Covid, we are supporting our customers with repositioning, keeping fleet availability high and maintaining our equipment to support the recovery.
Lastly, as we have communicated about this extensively over the past few years, Unilode believes that digitalisation will enable track and trace much more efficiently and add new revenue streams to the business of airlines, ground handlers, forwarders and other supply chain players.
Give us a sense of the partnership that you have with airlines around the world for ULD leasing and management?
At present Unilode provides ULD management solutions to 45 airlines from a fleet of close to 150,000 containers and pallets, which is almost 15 percent of the entire ULD fleet in the market. Most of our ULD management customers have chosen Unilode’s asset sharing model with pooling synergy benefits where all ULDs are branded with our R7 IATA ID code and are used interchangeably by our pooling customers as and when they are needed. This sustainable model provides them with more flexibility and operational efficiency especially when stock requirements change due to various reasons. A few other airlines prefer our hybrid ULD management option where the containers are dedicated for the airline’s own use and the pallets are part of the Unilode pool.
Our leasing business has significantly grown this year and provided ULDs on an ad-hoc basis to around 100 customers. We have increased our network and have pallet and container stocks at key stations in Europe, Asia and the USA.
What are some of the key highlights of your digital transformation strategies in the recent years? And how does the current crisis accelerate your digitalisation strategies?
We have started deploying Unilode’s digital strategy two years ago as we needed more transparency on the whereabouts of our ULD fleet in a business environment with many players along the supply chain. With our digital strategy we increase automation and although this requires initial investments, in the long run it reduces manual efforts and costs. We are currently in a full worldwide tag deployment programme for our entire fleet with over 50 MRO stations involved in the digitisation of containers and pallets. Today we have almost 40,000 digital units in our ULD network and this continues to grow at a quick rate.
Our digitalisation programme has been planned before the crisis and we continue to digitalise at full capacity. In the aviation industry we observe two trends around digital tracking: airlines want to use digital ULDs to reduce costs and use sensor data, for example, for temperature tracking. Our digital solutions address both challenges and we expect that the introduction of digital units in the market will accelerate because of the crisis and airlines will use digital tracking on a larger scale.
One of the important value additions that shippers and airlines are looking for is the ability to track and trace ULDs; there has been lot of effort by Unilode in deploying artificial intelligence and internet of things to ensure total visibility of your fleet. Could you give us an update on some of these new innovations?
Location track and trace is the main feature of our solution, but we also track temperature, humidity, air pressure, shock and opening of containers. Digital tracking helps us to further reduce human intervention in operations and generate accurate data through the supply chain. For example, stock control messaging will become an automated process. With digital tracking we are also automating milestone reports of a ULD on its journey. This includes storage periods in cool rooms, departure and arrival information and even in-flight data. Our customers will not only gain transparency through the supply chain, they will also be able to reduce cost through automation. This will result in a completely new way of doing business.
Benoit Dumont, chief executive officer, Unilode
What is the future for your in-house, custom-built IT platform FAST? You have partnered with Swissport, Menzies and dnata to install digital ULD readers that are connected to FAST – do you intend to widen this coverage to other cargo ground handlers and across all their warehouses?
Our worldwide reader network continues to grow with our digitalised ULD fleet and over 45 airline networks. Moving forward, we will have covered over 250 airports and the number of stations will increase with more airlines using Unilode’s digital service. Our global ground handling partners play an important role in expanding our network but we are also integrating local ground handling agents at many airports. Furthermore, we are installing readers in forwarders’ warehouses to cover the supply chain beyond airport fences. Besides our fixed readers, we will also start deploying Unilode’s mobile reader app. The app can be installed on mobile phones and tablets and performs scans within predefined geo fences. This solution will help us to rapidly expand our reader network and provide direct mobile access to digital information. With our FAST ecosystem, we have built flexible and powerful access to digital data directly whenever or wherever customers want. Moving forward we will implement other features to further increase supply chain transparency.
How can Unilode support the upcoming Covid-19 vaccine distribution efforts?
All three business units of Unilode, namely ULD (both management and leasing), MRO and Digital Solutions, can contribute to mitigate the upcoming vaccine distribution challenges. As some vaccines can be transported in passive temperature-controlled shipping containers and then loaded into a standard ULD, which can also be used to transport healthcare equipment and products, we continue to ensure that sufficient stocks are at our ULD management and leasing customers’ disposal when and where needed.
Unilode’s MRO business unit enables quick repair turnaround times for the ULDs and can provide additional repair capacity at key pharmaceutical hubs to support the supply chain. We have a longstanding partnership with Envirotainer and have recently announced the development of joint initiatives that includes the setup of pop-up ground handling and repair shops at key locations such as Beijing to help increase their active temperature-controlled container capacity. Additionally, our Digital Solutions, especially due to the temperature-measuring feature of the digitised ULDs, can help mitigate the upcoming vaccine distribution challenges.
All our service innovations and operational support demonstrate Unilode’s can-do attitude and diversification efforts as we look for opportunities to add value to our partners’ business and play an important part also in the pharmaceutical supply chain as the world prepares for the distribution of the Covid-19 vaccine.