FROM MAGAZINE: ULDs make a 'smart' move
Over the last decade, outsourcing of ULD ownership and management has seen a significant increase and is expected to continue growing as airlines subcontract non-core activities. With technology up their sleeve, third party ULD management companies are now trying to smarten ULDs which are generally considered as “dumb boxes” thus offering a complete solution for […]
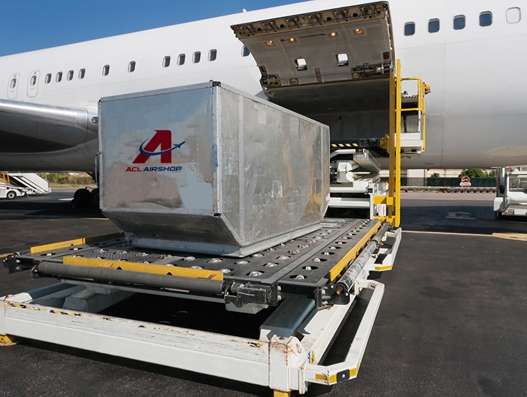
Over the last decade, outsourcing of ULD ownership and management has seen a significant increase and is expected to continue growing as airlines subcontract non-core activities. With technology up their sleeve, third party ULD management companies are now trying to smarten ULDs which are generally considered as “dumb boxes” thus offering a complete solution for their customers.
Surya Kannoth
Technology is continuously innovating to challenge how things are done today, and remains one of the critical success factors for professional ULD management.
The discussion of tracking and tracing ULDs with the help of technologies like GPS and Bluetooth has been on the airlines agenda for a very long time. The question is: what information do airlines need when it comes to tracking ULDs? And what more do third party ULD management companies need to do to make ULDs “smart enough”.
“Both Boeing and Airbus have limited the use of any transmitting for a long time, but recently we see changes in their standpoints and are finally allowing third party technology on board. There are many options in the market, but may not always offer a complete solution for every airline as there is need for critical mass and uniformity,” shares Jos Jacobsen, International GM for ULD Leasing & Sales, ACL Airshop.
Equipping ULDs with sensors that are able to “talk to airplanes” while in the bellyhold are some of the innovations that are in the development phase. Bob Rogers, senior advisor with Nordisk Aviation Products, spoke of how ‘smart’ ULD trials are currently underway during the recently concluded IATA World Cargo Symposium 2017 in Abu Dhabi.
Rogers further adds, “The ULD has always been a dumb box but it has the potential to be a smart piece of equipment which is able to transfer information between parties that is currently being put on a piece of paper.”
With the growth in ecommerce, customers’ demands have grown to wanting more detailed information down to the minute on their order. It is this growth that has led to the demand for smart ULDs. And for a smart ULD to function and deliver, collaboration within the supply chain holds key. “A smart ULD cannot do anything in isolation. The secret lies in the collaboration within the value chain. If you order something online, you want to know its status at all times. If a ULD can tell us at the very beginning that a certain product within it is broken, the store or the retailer can immediately advise you that it needs to be resent rather than having to wait till the product is delivered. The presence of a smart ULD will definitely help the consumer at the very end. In the first place, it will effect the airline, the forwarder and then us. I think that’s the next step,” explains Martin Kraemer, head of marketing and PR, Jettainer.
“Ecommerce is encouraging innovation within the ULD community and has already triggered smarter processes. With every single piece of cargo and ecommerce order being tracked, the ULD itself cannot be simply tracked on a written piece of paper,” says Jacobsen.
However, cost remains a concern when it comes to implementing such expensive technologies.
“When you look at cargo pallets, by themselves having a low value and the cargo they are carrying is not always high revenue, how do you justify the cost of implementing this technology immediately? You can determine the potential need of smart ULDs depending on what cargo you move, which destinations you fly to and the losses of pallets you may incur during the year,” he adds.
With cool containers, for instance, there is more demand for details like temperature, sudden movements, weight etc. High revenue cargo is also transported the same way which is why justifying the cost of implementing tracking devices becomes easier.
According to an IATA study, there are around 900,000 aircraft ULDs in service, representing a replacement value of over $1 billion; making ULDs expensive assets that require correct handling.
Push for innovations
Stepping up its efforts in innovation, Jettainer in association with Lufthansa Industry Solutions is developing ‘digital containers’. Announced at the 33rd International Supply Chain Conference in Berlin, the objective of the partnership is to create an “intelligent” container, trackable at all times and capable of measuring temperature changes, shocks and other external variables of its own accord, as well as reporting all information regarding its status.
“The intelligent container will ensure greater transparency within the process chain in future. We’re deliberately breaking new ground here in order to make our services for customers even more efficient in future,” commented Carsten Hernig, managing director of Jettainer in a statement.
The “smart” containers will not only offer to speed up maintenance and control procedures, but also increase the level of transparency of the ULD’s journey, making it easier to determine responsibility for any damage that occurs in transit. It is hoped that this capability will motivate companies to take greater care when handling containers and therefore serve to minimise the incidence of damage.
Meanwhile, ACL Airshop is constantly developing ways to control ULDs and collect information. ACL Airshop has developed their own stand-alone repair software solution in which one can easily report the amount of damages, locate where damages occur and account for the total cost of ownership - all specified per manufacturer or type. This information can be shared through an interface with any third-party software.
With the help of actual ULD Controllers, ACL Airshop has developed a web based ULD tracking system where ULDs can be tracked 24/7. The system shows historical data and can advise on station performance and assist with upcoming shortages or overstock. Currently, ACL Airshop is developing a new standard to track ULDs which can communicate with both existing software solutions.
Training staff for ULD handling
Last year, Jettainer, the Frankfurt-headquartered provider of outsourced unit load device (ULD) management services launched JettCare, a programme to create awareness for the value and importance of air freight containers and pallets. This involves training ground services staff, making them “ULD-X-Perts”.
In the specially developed training course, participants learn how to handle ULDs correctly, prevent damages and understand the operational and financial effects of any faulty or missing ULDs. Those who successfully complete the training programme receive a “ULD-X-Pert”-certificate.
“With the support of our competent partner by our side Lufthansa Industry Solutions, we believe we will have better solutions for the future,” said Thorsten Reikert, director-sales, Jettainer.
Outsourcing ULD management
The unit load device market is one of sunrise sectors within the airfreight industry, which is witnessing significant growth, as airlines continue to outsource their management to save on costs and improve efficiencies.
Outsourced ULD management provides a strong value proposition to airlines, primarily through significant cost and investment savings as well as operational efficiency improvements, while they focus on the core business of flying passengers and cargo.
In a recent development, Saudia and Saudia Cargo awarded the management of their containers and pallets to Unilode Aviation Solutions, erstwhile CHEP Aerospace Solutions, with operations set to start on April 1. Unilode will set up a regional ULD management office in the airlines' hubs in Jeddah and Riyadh, and will operate a repair shop in Jeddah for the maintenance and repair of ULDs and galley carts. As an additional service, Unilode will undertake the management of ULD accessories. Jettainer vouches on growing organically with its existing customers. “We are not just growing in terms of new customers; we had a very good year because we are growing with existing customers. Thus, we are growing organically which means if Lufthansa or American Airlines is growing, we grow with them. Last year, we added some smaller customers,” said Kraemer. In February this year, Jettainer took over the management and maintenance of Brussels Airlines’ unit load devices.
With the increased usage of wide-bodied aircraft, the ULD market remains buoyant and continues to evolve. With constant innovations in the ULD space, the market shows no signs of slowing down.