FROM MAGAZINE: Challenges faced by the aerospace logistics community
Are there gaps in aerospace logistics industry when compared with other industries? Ranjeet Sarai, vice president of aviation and aerospace at Kuehne+Nagel (Asia Pacific), argues in the affirmative and recommends very specific solutions to address the crucial challenges of the aerospace logistics industry. The aerospace industry is heavily regulated and focused on airworthiness and safety. […]
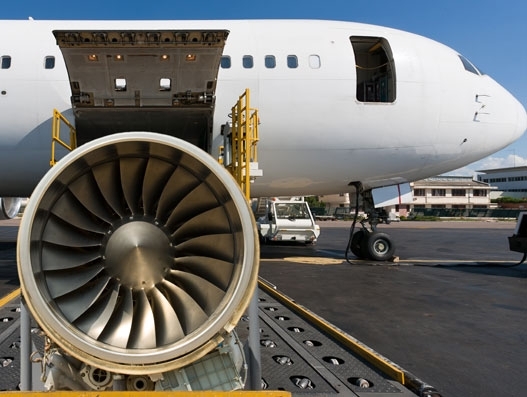
Are there gaps in aerospace logistics industry when compared with other industries?
Ranjeet Sarai, vice president of aviation and aerospace at Kuehne+Nagel (Asia Pacific), argues in the affirmative and recommends very specific solutions to address the crucial challenges of the aerospace logistics industry.
The aerospace industry is heavily regulated and focused on airworthiness and safety. So is everything satisfactory? In short, the answer is no. There is a considerable gap with the aerospace logistics community when compared to other industries. Automotive and high-tech are verticals where connected work groups operate to a streamlined process and people work in a different manner. Build to order or build to stock as such, the material flow is predictable. Aerospace logistics falls far behind and its complexity is underestimated.
This article focuses on three crucial elements that illustrate Kuehne + Nagel’s perspective on how to address the challenges confronting the aerospace logistics community: Customer, Technology and People. These have in turn shaped and formulated a global aligned strategy, focusing on the civil aviation market.
The customer: the passenger
Today the world is truly connected. Passengers as well as cargo are transported across borders at an unprecedented rate and at rapid pace. The availability of transportation options has created a highly complex and competitive marketplace, in turn placing considerable strains on the supply chain.
Passengers are able to access accurate and timely information on key decision criteria for selecting carriers: transit time, the comfort of the cabins, in-flight service and dining experience against achieved performance and cost. For the more seasoned traveller, they will also take into consideration the aircraft type, age of the fleet, enhanced IFE and connectivity options. This has increased the push to modernise existing fleets.
Carriers skirmish to attract and retain customers yet any delays will influence a customer’s decision on carrier selection. The key theme here is that the passenger is at the forefront of the mind when considering aerospace logistics.
How you can pull it all together: Technology
In this day and age, accurate, timely access to real time information is a precondition. With multiple stakeholders involved in the supply chain, from order placement to the return loop, how do you manage the flow of information and provide proactive notifications in order to keep an already diminishing resource pool productive and not waiting on call backs and follow ups for critical shipment information?
In other manufacturing sectors, the supply chain is synchronised and orchestrated to deliver product at defined intervals to named sites on certain days and at specified time. The manufacturing side maintains a close vigil on the movement of material, barring of course the impromptu bumps in the supply chain for shortages and seasonal challenges.
In aerospace, the challenge starts with the unscheduled events. It is not unusual for a narrow body aircraft to operate over 40 flights, serve upwards of 15 destinations and travel over 40,000 kilometre in a week. A wide body would operate over a dozen flights, across several destinations and cover more than 60,000 kilometre. At any time and almost anywhere a part may be needed, passengers are often left stranded in a terminal, sometimes in an unfamiliar airport with no end in sight. It is these events that impact the passenger travel experience and where technology plays a vital role helping ensure real time data is available to help make the appropriate arrangements.
And how this is all packaged together: The people
Responsiveness and delivering a practical round-the-clock solution is paramount to customers. In this context, we refer to the airline. With hundreds of passengers, potentially over a thousand can be impacted with knock-on delays to schedules if the committed solution is not provided.
The customer who places the booking needs to be assured that the movement of parts or components is being handled in the most appropriate manner. Whether it is a one kilogram AOG (aircraft on ground) part that is hand carried or an oversized engine that may move across multiple modes of transport, the people need to be ‘certified aerospace logistics’ professionals.
Individuals who can assess the end-to-end move, taking into account, but not limited to: seasonality, capacity constraints and schedule integrity, security and regulatory challenges.
With the growing challenges in the industry, companies need to ensure they have the most customer centric, forward-thinking and collaborative workforce. Multiple parties are involved in a typical move, in many instances logistics services providers need to work with direct competitors. The competitive spirit needs to be put aside and place the passenger at forefront of mind. The organisational leadership needs to instill the spirit and lead by example.
Piecing it all together: Supply the Sky
Over the past 30 years, Kuehne + Nagel has invested in each of the three critical aspects: Customer, Technology and People. We work closely with our customers across the entire lifecycle of aerospace logistics to shape, deploy and enhance our products and tools to deliver market-leading solutions. Supply the Sky is our customised, nose-to-tail supply chain solutions that provide aerospace manufacturers, airlines and service suppliers with proven, best-in-class processes as well as powerful information technology.
From working with the leading global aerospace and defence related services, OEMs, engine manufacturers and MROs across all regions, we have developed KN EngineChain to move engines, KN InteriorChain to support customers with cabin retrofits and KN SparesChain to move spare parts providing predictive and repeatable solutions with end-to-end real time visibility.
Our in-house team of dedicated IT professionals build user friendly applications and web tools to provide end-to-end visibility across all modes of transport. With powerful search possibilities and customisation like free text search and pre-defined filters, it eases the work for our customers.
Aside from standard information on content, detailed information on shipper, consignee and potentially additional parties, commercial and shipping documents, we also work with customers on online data providing the physical monitoring data: temperature, humidity, shock, etc. in our Enterprise Visibility tool.
By selecting and positioning the people into the right functions, we are able to understand the customer’s needs, articulate and document specific requirements in the form of detailed working instructions. Supporting roles in the areas of quality, health, safety and environment are intricately involved in the development of the solutions resulting in certified logistics that exceed the most stringent industry standards.
The supply chain today is very different to the supply chain of yesteryear; the supply chain of tomorrow will evolve and it is evident the industry supporting the needs is not evolving at the same pace.