Airbus gears up for A350 freighter final assembly
Airbus is preparing for the final assembly of its A350 freighter, with key components and FAL stations updated.
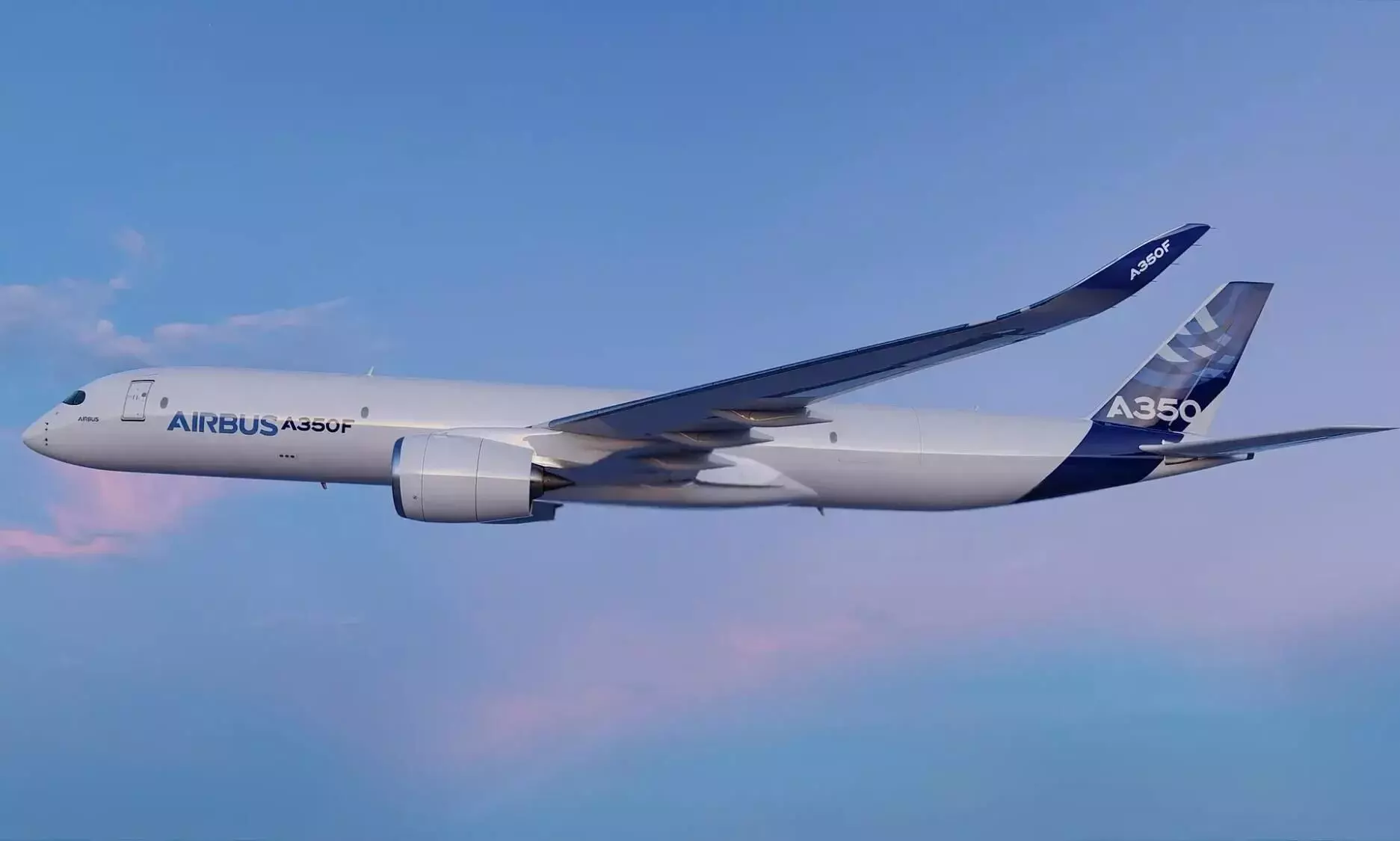
European aircraft manufacturer Airbus is gearing up for the final assembly of its first A350 freighter. Significant progress has been made, with large components of the aircraft already under production at Airbus Atlantic and Airbus Aerostructures in France and Germany.
Meanwhile, preparations at the Roger Béteille Final Assembly Line (FAL) in Toulouse are nearing completion. The A350F, the latest addition to the A350 Family, combines substantial design commonality with its passenger counterparts but introduces critical structural adaptations, according to an official release from Airbus.
A350F is the third member of the A350 family after the existing passenger variants A350-900 and A350-1000.
Airbus states that the freighter's fuselage length is optimised to fall between the extended A350-1000 and the standard A350-900. Additionally, the aircraft is equipped with the largest main-deck cargo door ever installed on a commercial aircraft, positioned on the left side of the rear fuselage.
Inside, the freighter is equipped with a full-length cargo-loading system to accommodate containers and pallets, while the sidewalls are reinforced with a windowless lining. Significant design modifications at the front include a 9g cargo barrier wall, behind which are a dedicated Flight Crew Rest Compartment (FCRC) and a courier area.
To accommodate these changes, Airbus has retrofitted eight FAL stations, installing new jigs, adaptable platforms, and tools. Emmanuel Royer, Airbus’ A350F FAL industrial lead, says, “We had to transform our stations by positioning special jigs and a tower to allow people to access the main deck cargo door and also permit trolleys into the aircraft through the door.”
Staff using the adaptable platform at Station 50 to access the A350 freighter’s main-deck cargo door and fuselage. (Image: Airbus)
At ‘Station 50’ in the FAL, the A350 fuselage join-up is completed along with component integration. At ‘Station 40,’ where wing assembly and interior installation occur, a new platform plug with a lift is being tested to position cargo systems near the main deck entrance for the freighter variant.
Close-up of the new adaptable platform installed at Station 50 in the A350 FAL. (Image: Airbus)
At ‘Station 30,’ where ground tests and interior pre-customisation take place, the Main Deck Cargo Door (MDCD) platform plug allows access through the freighter door and supports door surround rigging and inspection.
“We reworked the concrete, the hardware, and the software to accommodate and manage the new fuselage length. Being able to change the jig length globally from one aircraft to another will therefore allow us to be flexible for -900, and -1000, and now the freighter,” says Royer.
Airbus is adapting both the A350 FAL stations and production processes for the A350 freighter. Using digital twins, the team simulates workflows to optimise assembly, particularly for the Ancra-supplied cargo loading system (CLS), which includes over 3,000 parts. Unlike the A330-200F, the CLS components will be directly embedded into the A350F’s floor grid. To assist with this complex task, Airbus is employing augmented-reality tools like 3D HoloLens glasses for real-time guidance. Additionally, a task force is preparing training materials to ensure the FAL teams are ready for the freighter's arrival.
Station 40, where the A350 family’s wing join-up and interior equipment installation occur. A new platform plug is being tested for the freighter variant. (Image: Airbus)
Alongside the physical updates to the A350 FAL stations, production teams are adapting their processes through co-design and co-development. Since the programme’s launch, teams have worked closely with the Airbus Design Office to define and integrate technical solutions, ensuring components meet industrial constraints.
For instance, the 9g barrier wall is being co-designed with Airbus Engineering and Turkish Aerospace, using a mini lifting system and trolley for installation. Similarly, teams are collaborating on the main-deck cargo door, cargo lining, and other freighter-specific features to finalise the design and testing processes, with most of the work completed in the past 12 months.
At Station 30, the A350F’s main-deck cargo door platform plug streamlines access for the inspection and rigging of the freighter door. (Image: Airbus)
The A350F ground testing strategy was defined early through co-design with design offices and Chief Engineer teams, focusing on safety, ergonomics, accessibility, and test strategies. This approach ensures minimal disruption when switching between freighter and passenger configurations. For instance, the CLS installation will undergo thorough testing, including full system checks with pallets and loads to validate functionality.
Looking ahead, summing-up the current status and next steps, Royer says: “As well as finalising the readiness of our jigs and tools over the next six months, we will also finalise all the instructions and work orders to prepare our teams, train our workers and to secure that everybody is ready with everything in place for the A350F FAL start.”
This report is based on a story published on the Airbus website, the original story can be found here.